Alpha Metals Omega Meter
600R-SC Omega Meter
S/N: 6031
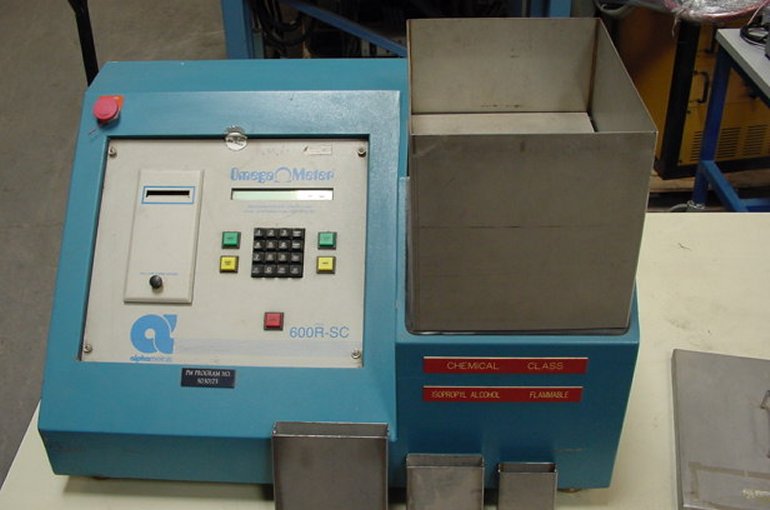
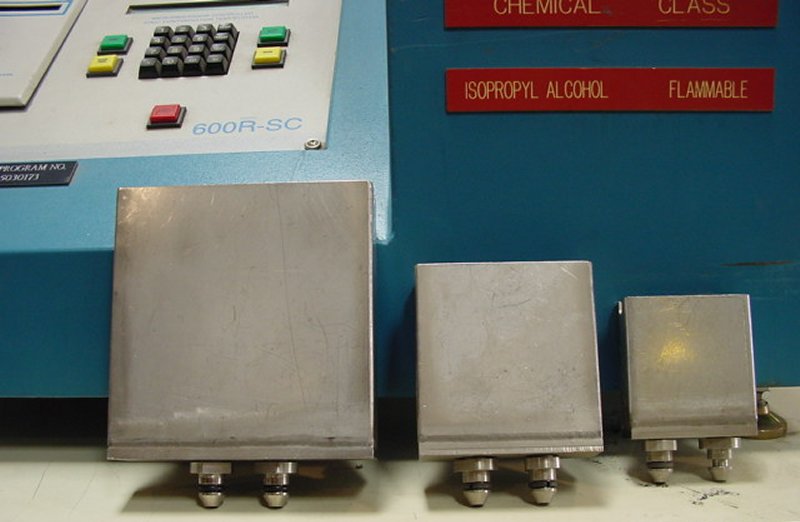
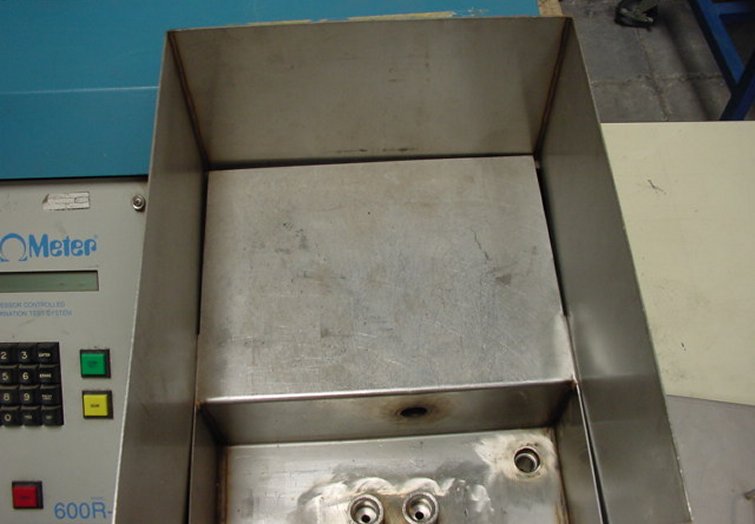
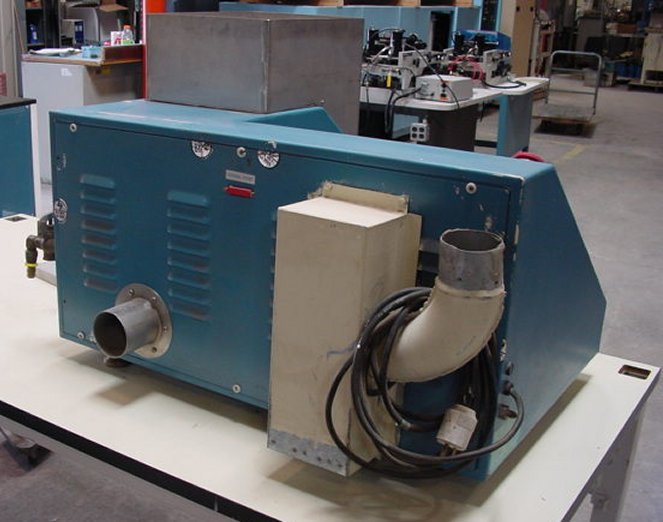
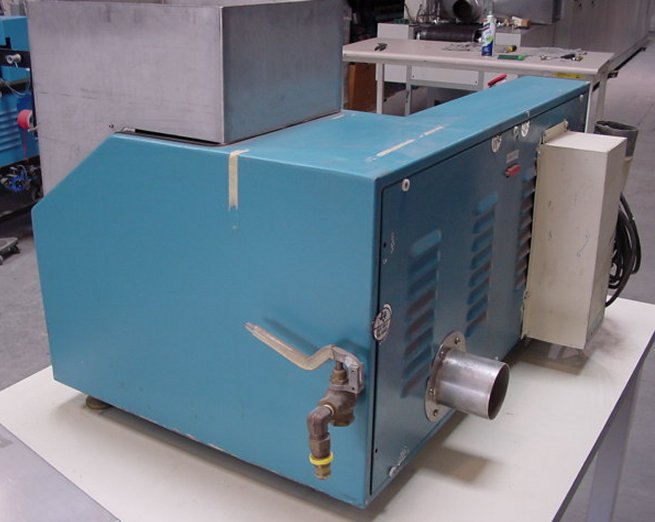
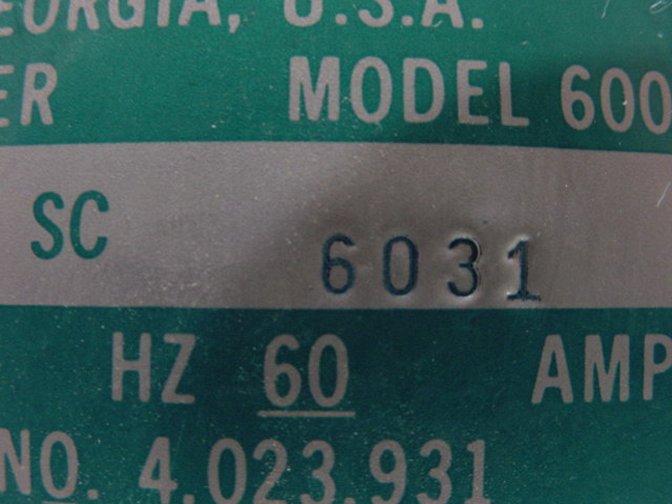
Alpha Metals Omega Meter
Model 600R Description
The Alpha Metals Omega Meter is microprocessor controlled ionic contamination test system designed to perform cleanliness testing on printed circuit boards and other parts. The Alpha Metals Omega Meter is used to determine the quantity of ionic contamination on a specimen under test, typically a printed circuit board (PCB).
The fabrication of printed circuit boards and the subsequent assembly of printed wiring assemblies includes processes where corrosive ionic materials are introduced to the board and assembly package. Examples of corrosive ionic elements include Chemical Etchants, Plating Salts, Chemical Metal Cleaners, Solder Fusing Chemicals, Soldering Fluxes, Human Perspiration and Hand Lotion, Chemical Products and Environmental Fallout.
Ionic contamination represents one of the most significant factors causing degradation and failure of electronic assemblies. Very small residual quantities of ionic contamination from numerous and varied sources affect reliability and can cause catastrophic failure of components and circuits. Residual ionic contamination can cause surface electrical leakage and chemical, galvanic and electrolytic corrosion.
Key to reducing failures due to ionic contamination is cleaning. The Omega Meter tests to determine that a board, component or printed-wiring assembly is, in fact, clean. The electrical resistivity of a known volume of an aqueous solution represents the direct measurement of levels of ionic contaminant present in the solution. Quantitative measurements of ionic contamination on parts can be made by measuring the electrical resistivity of a known volume of rinse solution used to extract and remove the ionizable contaminant from the known surface area of the sample being tested. The extract solution must be of an extremely high level of purity.
The Omega Meter System is an automated process. A wash solution of 75% by volume of ACS reagent grade isopropyl alcohol and 25% by volume of distilled water is measured into the test cell through a set of D.I. columns to achieve a resistivity exceeding 20 megohm centimeter. Other formulations of alcohol and water including D.I. water alone may be used to comply with special test requirements. A sample component or assembly is submerged into the clean test solution and the solution is agitated to promote removal and solubilization of all ionic residues from the test sample. The change in resistivity is continuously monitored and displayed on the LCD display on the console. Knowing the area of the sample in inches, the volume of solution in millimeters and the resistivity in megohms, the system automatically calculates the contamination that has been added to the solution in "micrograms" of equivalent sodium chloride per square inch. When the test is completed, the test parameters are printed along with the total contamination extracted from the test sample. Contaminated test solution is regenerated through the D.I. columns to obtain the required purity for reuse in subsequent tests. The closed loop Omega Meter System may be used for many months of testing with minimal addition of fresh solution.
Typically the contamination on the PCB would be process residues from the fabrication of the circuit board or from the board assembly process. Measure this contamination to be sure that the cleaning steps in making the PCB or assembling the PCB are properly removing the process chemical residues. You can perform this test by placing the PCB specimen in the Test Cell (the large Plexiglass container on the top of the unit). The system then fills the Test Cell with an isolated volume of IPA/Water test solution (not included). This solution is heated and agitated and removes any contamination on the PCB. The ionic contamination is then determined by monitoring the resistivity of the test solution. The Omega Meter then provides a printout of the results using the embedded printer located on the front panel.
This type of equipment is normally used in a manufacturing facility to measure printed circuit boards contamination as part of printed circuit board fabrication and/or assembly operations.